F8e0 Error Code
Duet Troubleshooting Guide
Duet Diagnostic Test Mode
Duet Error Codes
Duet Part Testing | Duet Wire Diagram
I believe the control will need to be replaced. Of course, check the wiring from the fan to the board first. The link below is to the part you will need from a highly recommended company rated A+ with the Better Business Bureau. Once the oven reached approx 200 o, a code (F8E0) appeared on the digital display along with the error 'Cooling Fan Speed Too Low'. I pulled the oven away from the wall and followed the instructions on the service manual:.1.Unplug range or disconnect power. 2.Pull the range forward and remove the top access cover. 0x80192f76 seems to indicate that the connectivity with credential occurs some issue. For such kind of issue, we may need to collect deeper logs or traces to analysis, I would recommend to create an online support ticket.
WFW70HE, WFW80HE, WFW81HE, WFW94HE, WFW95HE, WFW96HE, WFW97HE (Non Steam)
WFW8640, WFW86HE, WFW8740, WFW87HE, WFW88HE (Steam)
Hello F8E0 is a Cooling Fan Speed Too Low Fan speed below 500 rpm, either because the fan is spinning too slowly or because there is a problem with the Hall Effect sensor. See complete diagnostics link below.
Duet Washer Error / Fault Codes
Once you are in the Duet Washer's Diagnostic Mode momentarily press the 3rd button you used to enter diagnostics, and the washer will display the last 4 fault codes one button press at a time. There are a few helpful things to note here. If the Duet successfully runs 10 cycles in a row with no fault the error will be cleared from the washer's memory, so any errors you see are likely new and active.
After you have recorded any stored errors you can clear the code by pressing and holding the 3rd diagnostics button for 5 seconds. If there are no stored errors 888 will be displayed with 3 beeps.
Duet Washer error and fault codes are displayed by alternating F#__ and E#__ The F error describes the washer system and the E error further defines the washer part that may be having a problem. F1, F2, F6 Are main control and program faults. F3 faults are washer sensor related problems. F5 faults are door lock and door switch related duet codes. F7 Faults are motor and motor control related problems. F8 Faults are water related… valve, dispensing system, water level, steam valve, and flow meter problems. Lastly F9 faults are related to the washer's ability to drain.

NOTE: 'Anytime I say unplug and check connections' or something like that...
It also means unplug the washer so you don't get electrocuted!
- Your Duet washer has detected that it is full of soap suds which are difficult to drain. Or perhaps your Duet washer wants a beer… This can be caused by using non HE washer detergent, using too much soap, or possibly a drain pump or pressure sensing problem.
- Your Duet washer has detected a load during a washer cleaning cycle. If this does not appear to be the case you may have mechanical friction causing drag when the inner washer drum is rotating.
- This is a bad one… Duet washer main control error. Try unplugging the washer for a minute and putting the washer through a quick diagnostic test and see what you get… In some cases this can reset the control and buy you some time.
- The motor control board (MCU) has attempted to reset several times and does not like the result. (Duet Washer Motor Tests)
- This is a rare one but it means that something is wrong with the washer cycle that was selected. Put your Duet washer through the UI Tests, and check all of the connections to the control. your washer may need a new main control board.
- Check the pressure sensing hose for kinks or blockage. You will also want to check the pressure sensor (Duet Washer Pressure Sensor Check)
- This error will display if the washer's temperature sensor is out of range. (23º - 217º) check all wire connections from control to the washer temp sensor. I have had several of these become unplugged at the sensor connection at the back of the washer drum. (Duet Washer Temperature Sensor Check)
- Possible causes…
1. Your Duet washer has a bad door switch.
2. You have not opened to door for 3 wash cycles… (Too many Margarita!?)
3. Trying to start a cycle when the washer door is open. (Duet Washer Door Switch Check) - Your Duet washer was not able to lock the door after 6 times… you can't say it didn't try. Check that the tab on the washer's door that inserts into the door lock is not broken, that it's properly aligned with the door lock hole, and that there is nothing that may be jamming the lock. (Duet Washer Door Lock Check)
- Your Duet washer was not able to unlock after 6 tries. Check that the tab on the washer's door that inserts into the door lock is not broken, that it's properly aligned with the door lock hole, and that there is nothing that may be jamming the lock.
- Communication error between the main control and the motor control. Check all the wire connections from the CCU to the MSU for good connection. If everything looks good, check for broken wires with a multi meter.
- Communication fault between the main control board (CCU) and the user interface (UI) unplug and check the wire connections between the washer's (CCU) and the washer's (UI)
- Make sure the inner drum turns freely. (There may be some magnetic resistance (Magnetic Motor) but there should be no mechanical drag.)) (Duet Washer Motor Check)
- Check that water is getting to the steam valve, it may be blocked or restricted.
- Your Duet washer has tried to fill for 13 minutes but has not sensed any water entering the tub… Are your home valves turned on? Is the drain hose too far down the drain pipe? If the end of the drain hose is below the water level in the washer, water can siphon out as fast as it goes in. Check water valve electrical connections before changing out the valve.
- This means that the dispenser motor which directs fill water to the appropriate dispenser area, is not moving properly. take the top off and run the Duet Washer Quick Diagnostic Test, C03 checks the Duet washer's dispensing system.
- If this was real you are probably already aware of it… but hopefully your Duet washer's computer brain saved the day and drained the water out before your floor was ruined. If you get this error...
1. check that the washer's water valves are closing all the way and water is not filling into the tub when it shouldn't be. If water is slowly filling the tub even when the washer is unplugged you need to replace the washer fill valves. If it's filling quickly and it suddenly stops when you unplug the washer you may have a bad main control board.
2. Check that the drain pump is working properly.
3. Check the pressure sensor. - Not even 0.1 L of water has entered the tub from the first 30 seconds of the Duet Washer Quick Test… Is the water turned on?
- This is the most common Duet washer error code! The F9E1 long drain error is referring to duration not length. if it takes longer than 8 minutes to drain your highly water efficient washer then ether the drain system is pugged up with who knows what or the drain pump is having a problem. The best way I have found to deal with the water when your washer's drain pump isn't working is to use a shop vac and pull from the drain hose. If that works the your pump is highly suspect. If it doesn't work then you almost certainly have a clog in your Duet washer's drain system and the pump may be fine.
SUDS Error - Suds fault.
F0E1 Error - Load detected during a clean cycle fault.
F1E1 Error - Main control fault.
F1E2 Error - Motor control fault.
F2E3 Error - Cycle fault.
F3E1 Error - Pressure switch/ sensor fault.
F3E2 Error - Temperature sensor fault.
F5E1 Error - Door switch fault.
F5E2 Error - Door lock fault.
F5E3 Error - Door unlock fault.
F6E2 Error - Communication fault.
F6E2 and F6E3 Errors - Communication fault
F7E2 Error - Motor or motor control board fault.
F8E0 Error - (Steam models) Steam valve fault.
F8E1 Error - Water fill fault.
F8E2 Error Dispenser fault.
F8E3 Error - Overflow fault.
F8E4 Error - Flow meter fault.
F9E1 Error - Long drain fault.
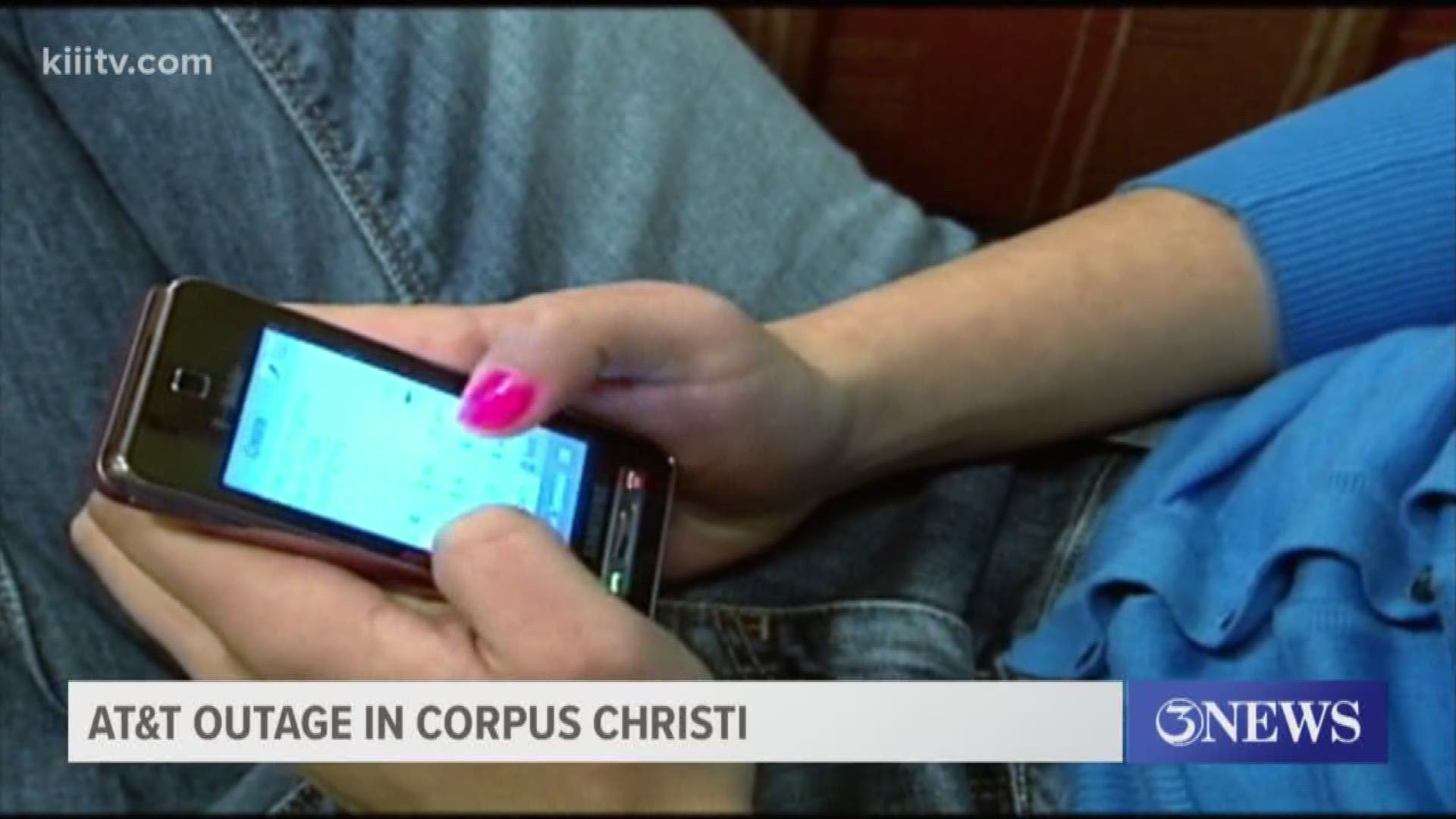
Clear Stored Duet Error & Fault Codes
Not all washer made by Whirlpool have the ability to clear error code memory. Thankfully this style does... Once you are in the Duet washer's diagnostic mode and have recorded any errors that the washer has in it's little computer brain, press and hold the 3rd button used to enter diagnostics for 5 seconds... Like it never happened : )
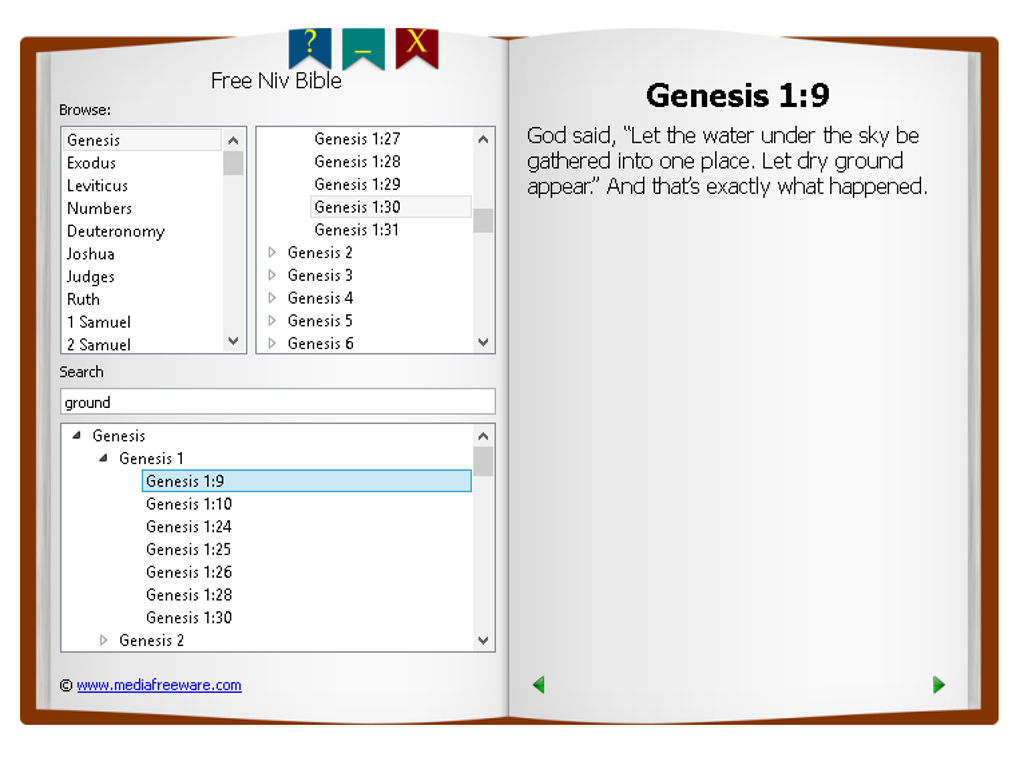
Problem | Solution |
---|---|
Nothing will operate | ■ Household fuse blown or circuit breaker tripped? Replace the fuse or reset the circuit breaker. If the problem continues, call an electrician. ■ Is the main or regulator gas shutoff valve in the off position? ■ Is the range properly connected to the gas supply? |
Surface burners will not operate | ■ Is this the first time the surface burners have been used? Turn on any one of the surface burner knobs to release air from the gas lines. ■ Is the control knob set correctly? Push in knob before turning to a setting. ■ Are the burner ports clogged? |
Surface burner flames are uneven, yellow and/or noisy | ■ Are the burner ports clogged? ■ Are the burner caps positioned properly? ■ Is propane gas being used? The range may have been converted improperly. |
Surface burner makes popping noises | ■ Is the burner wet? Let it dry. |
Excessive heat around cookware on cooktop | ■ Is the cookware the proper size? Use cookware about the same size as the surface cooking area, element or surface burner. Cookware should not extend more than ½' (1.3 cm) outside the cooking area. |
Cooktop cooking results not what expected | ■ Is the proper cookware being used? ■ Is the control knob set to the proper heat level? ■ Is the range level? Level the range. |
Oven will not operate | ■ Is the electronic oven control set correctly? ■ Has a delay start been set? ■ On some models, is the Control Lock set? ■ On some models, is the Sabbath Mode set? |
Oven temperature too high or too low | ■ Does the oven temperature calibration need adjustment? |
Display shows messages | ■ Is the display showing “FAULT DETECTED?” A fault has been detected. Follow the displayed directions “PRESS ENTER TO TRY AGAIN” or “DISABLE POWER TO CLEAR.” If the fault does not clear, reappears, or “FEATURE NOT AVAILABLE” is displayed, call for assistance or service. ■ Is “SAb” flashing? Oven is in Sabbath Mode. To cancel, press and hold the SETUP pad for 5 seconds. |
Self-Cleaning cycle will not operate | ■ Is the oven door open? The display will show “CLOSE DOOR.” Close the oven door all the way. ■ Has the function been entered? ■ On some models, has a delay start Self-Clean cycle been set? ■ Has a delay start been set? ■ Is the control in Sabbath Mode? ■ Is the oven temperature above 400°F (205°C)? Let the oven cool before using the self-clean cycle. |
Oven cooking results not what expected | ■ Is the range level? Level the range. ■ Is the proper temperature set? Double-check the recipe in a reliable cookbook. ■ Is the proper oven temperature calibration set? ■ Was the oven preheated? ■ Is the proper bakeware being used? ■ Is the oven vent blocked? ■ Are the racks positioned properly? ■ Is there proper air circulation around bakeware? ■ Is the batter evenly distributed in the pan? Check that batter is level in the pan. ■ Is the proper length of time being used? Adjust cooking time. ■ Has the oven door been opened while cooking? Oven peeking releases oven heat and can result in longer cooking times. ■ Are baked items too brown on the bottom? Move rack to higher position in the oven. ■ Are pie crust edges browning early? Use aluminum foil to cover the edge of the crust and/or reduce baking temperature |
Broiling results not what expected | ■ Is there excessive smoking? Food may be too close to the broil element or may have excessive fat. Move rack to a lower position. ■ Is the oven door closed? Close oven door to the broil stop position. ■ Was the broil element preheated? Allow broil element to preheat for 5 minutes. |
Jenn-Air W132B oven troubleshooting
PROBLEM | POSSIBLE CAUSES | SUGGESTED CORRECTIONS |
---|---|---|
Part or all of appliance does not operate. | 1. Wall oven is disconnected from power or is loosely connected to power. | 1. Check to be sure plug is securely inserted into wall receptacle. |
2. Tripped circuit breaker or blown fuse. | 2. Check or re-set circuit breaker. Check or replace fuse. | |
3. Power supply has been interrupted. | 3. Wait until power has been restored. | |
4. Oven controls not set properly. | 4. Setting oven control. | |
5. Oven door left in locked position after clean cycle. | 5. Unlock oven door. | |
6. Oven set for delayed cook or clean. | 6. Cancel program. | |
7. Oven control lock-out feature is activated. | 7. deactivate this feature. | |
Oven elements fail to operate or heat food. | 1. Wall oven is disconnected from power or is loosely connected to power. | 1. Check to be sure plug is securely inserted into wall receptacle. |
2. Tripped circuit breaker or blown fuse. | 2. Check or re-set circuit breaker. Check or replace fuse. | |
3. Power supply has been interrupted. | 3. Wait until power has been restored. | |
4. Oven controls not set properly. | 4. setting oven control. | |
5. Oven was not set to correct temperature. | 5. Set oven to temperature recommended in recipe. | |
6. Oven was set for delayed cook. | 6. Cancel program and reset. | |
7. Oven was not preheated properly. | 7. Allow oven to preheat until PREHEAT indicator turns off and a beep is heard. Then place food in oven. | |
8. Defective part. | 8. Have authorized servicer replace part. | |
Baking results differ from previous oven. | 1. Oven seems hotter or cooler than your previous oven. | |
Baking results are not what you expected. •Uneven browning (too dark on top or bottom). •Underdone or overdone. •Browning is too dark or light. •Cake is not level. | 1. Oven is too hot or too cool. | 1. Select correct oven temperature. When baking, always preheat oven before adding food. |
2. Selected BROIL rather than BAKE. | 2. Select the BAKE pad, not BROIL, for baking. | |
3. Food not positioned correctly in oven. | ||
4. Used incorrect pan. | 4. Dark pans produce dark browning. Select shiny aluminum pans or reduce the oven temperature by 25°F. | |
5. Used aluminum foil incorrectly. | 5. Never use foil to cover an oven rack. Place a small piece of foil on the rack below the rack holding the pan. | |
6. Oven rack was crowded with pans. | 6. Stagger pans on rack. Allow 1 to 2-inches between pans and oven walls. | |
7. Used unreliable recipe or did not follow recipe. | 7. Select recipes from reliable sources. Read and carefully follow instructions and do not substitute ingredients. | |
8. Oven vent was blocked. | ||
9. Door is not correctly installed. | ||
Food not broiling properly. | 1. Oven incorrectly set. | |
2. Used incorrect rack position. | ||
3. Broil element was not preheated. | 3. For optimum browning, preheat the broil element for 3 to 4 minutes before placing food in the oven. | |
4. Used aluminum foil incorrectly. | 4. The broiler pan can be lined with foil; never line the broiler insert with foil. | |
5. Oven door was dosed during broiling. | 5. Always leave door opened to the broil stop position (opened about 4-ir>ches) during broiling. | |
Oven smokes excessively during broiling. | 1. Food placed too close to broil element. | 1. Move broiler pan down one rack position. |
2. Broiler insert covered with aluminum foil. | 2. Never cover insert with foil as this prevents fat from draining to pan below. | |
3. Meat is too fatty. | 3. Trim excess fat before broiling. | |
4. Marinade not completely drained before broiling. | 4. Completely drain marinade from meat. | |
5. Basted meat too early during broiling. | 5. Baste meat during the last few minutes of cooking. | |
6. Used a soiled broiler pan. | 6. Always clean broiler pan and insert after use. | |
Oven will not self-clean. | 1. Self-clean feature was not properly set. | |
2. Oven set for a delayed clean. | 2. Cancel program and reset clean cycle. | |
3. Oven door not closed and/or locked. | 3. Close and lock oven door. | |
Oven door will not lock for self-clean. | 1. Self-clean was not properly set. | |
2. Oven door is not closed. | 2. Be sure door is properly closed. | |
Oven door will not unlock after clean cycle or if accidently locked during baking. | 1. Clean cycle ended less than one hour ago. | 1. Allow about 1 hour for oven to cool. Door can be unlocked when LOCK indicator is no longer displayed. |
2. Oven hot enough to engage internal lock, if accidently locked during baking. | 2. Allow oven to cool until LOCK indicator no longer is dispfayed. To speed cooling, allow a fan to blow on oven door. |
Jenn-Air W2451 oven troubleshooting
Problem | Cause |
---|---|
Test Access | The test mode can be accessed by holding the stop time key down at power up or by holding the stop time key down for 10 seconds within 5 minutes of power up mode. No other key can be pressed before the stop time key, that would block the test mode access. |
Test Exit | Exit the test mode by pushing the cancel key or test will self-terminate after 16 seconds from the last key command chosen. |
Test Function | Test mode is perfomed by pushing a keypad and testing for an output response. When the keypad is released, the output is terminated and the display will return to the display. The following is a list of key actions and responses. |
Bake Key | Activates bake relay on the power relay board. |
Broil Key | Activates broil relay on the power relay board. |
Convect Bake Key | Activates convect bake relay (CVBAK) on the power relay board. |
Convect Roast Key | Activates convect roast relay (CVRST) on the power relay board. |
Oven Light Key | Activates oven light (OVLT) relay on the power relay board. (See note 2 above.) |
Probe Key | Activates the display on the control to display the probe temperature. |
Timer Keys | Activates the display to show factory codes in the blue displayed digits and oven temperature in red. |
Clean Key | Activates blue display digits which shows the state of the door lock switches and the status of the user selectable options. |
Stop Time Key | Will activate the beeper 100% as long as the key is pressed. Also, it will display the control I.D. # in the blue time digits and the power relay board I.D. # in the red temperature digits. |
Clock Key | Activates all display segments to light. |
Cook Time Key | Activates any fault codes stored in the memory. The time digits display any fault codes for the membrane and control board. The temperature digits display any fault codes for the power relay board. NOTE: If 'FO' is displayed, there has not been anv fault codes sensed in that portion of the svstem. Anv stored fault code can be cleared to FO. after repairs have been made, by entering the fast test and pressing both the cook time and stop time keys for 5 seconds. |
Digital Input Keys | Activates the display to show the same digit (0-9) that is pressed. |
Temperature Offset Change | Program bake above 500°, repress bake pad and hold for 3-4 seconds, the pad must be re-pushed within 3 seconds. The digital keys can be used to set the offset between positive and negative(-). Entered values are rounded to the next 5° increment. (Example: pushing key 3 will display a 5° increment). |
Clock and Temperature Change | The clock can be set to be displayed in 24 hour form. Also, temperature can be displayed in degree 'C To access, hold either timer keys down on power up. The two left digits will display the format for the clock, the right digit will display 'F' or 'C.' The display can be toggled by pushing the bake or upper bake key to toggle the clock. The temperature display can be toggled from F to C by pushing the broil key or upper broil key on a double oven control. |
Jenn-Air ELECTRIC WALL oven troubleshooting
PROBLEM | SOLUTION |
---|---|
For most concerns, try these first. | • Check if oven controls have been properly set |
• Check if oven is properly connected to electrical outlet. | |
• Check or re-set circuit breaker. Check or replace fuse. | |
• Check power supply. | |
Clock, indicator words, and/or lights operate but oven does not heat. | • Clock controls may be set for a Cook/Hold or Delay function. |
• The Oven Control Lockout may have been set. | |
Oven light and/or clock does not function. | • The light bulb is loose or defective. |
• The oven light does not work during self-cleaning process. | |
• Oven may be in Sabbath Mode. | |
There is a strong odor or light smoke when oven is turned on. | • This is normal fora new wall oven and will disappear after a few uses. Initiating a clean cycle will “bum off” the smells more quickly. Turning on a ventilation fan will help remove the smoke and/or odor. |
• Excessive food soils on the oven bottom. Use a self-clean cycle. | |
Oven will not activate the self-cleaning process. | • Oven may be set for a delay clean. |
• Oven may be set for Sabbath Mode. | |
• Double wall ovens - only one oven cavity can be cleaned at one time. | |
Oven did not clean properly. | • Oven may need longer cleaning time. |
• Excessive spills were not removed prior to self-cleaning process. | |
Foods do not broil properly. | • Check rack position. |
• Voltage into house may be low. | |
Baked food is burned or too brown on top. | • Food may be positioned incorrectly in oven. |
• Oven not preheated properly. | |
Foods bake unevenly. | • The oven may be installed improperly. |
• Check the oven rack with a level. | |
• Stagger pans, do not allow pans to touch each other or oven wall. | |
• Check instructions for suggested placement of pans on oven rack. | |
• There may be too many pans on one rack. | |
• Baking pans may be oversized. | |
Oven door will not unlock. | • Oven may not have cooled to safe temperature after self-cleaning process. |
Oven baking results are less than expected. | • The pans being used may not be of the size or material recommended for best results. |
• There may not be sufficient room around sides of the pans for proper air circulation in the oven. | |
• Check instructions for preheating, rack position and oven temperature. | |
Baking results differ from previous oven. | • Oven thermostat calibration may differ between old and new ovens. Follow recipe and use the directions in this guide before calling for service since the calibration on the previous oven may have drifted to a too high or too low setting. |
Fan is heard when oven is turned on. | • This is the cooling fan and is normal. The fan will continue to run after use until the oven cools. |
Cooling fan continues to operate after the oven has been turned off. | • This is normal. The fan will automatically shut off when the oven has cooled. |
Probe does not work. (select models) | • Check to be sure probe plug is properly inserted into oven receptacle. |
• Probe may not be positioned in food properly. | |
• Probe temperature may have been improperly set | |
• Food may have been too cold or frozen when the probe was inserted. | |
Fault Codes | • The oven may detect a fault during programming or during operation. If a fault is detected, the message “Fault detected - press power to clear' or “Fault detected - press enter to try again” may appear. Follow directions in the display. If the fault reappears or does not clear, call an authorized servicer or the toll-free number in the display. |
• If the same operation is attempted before having the wall oven repaired, the message “Feature not available' will appear. The feature will remain inoperable until sen/ice is obtained. | |
• If the oven is heavily soiled, excessive flareups may result in a fault code during cleaning. Press the CANCEL pad and allow the oven to cool completely, wipe out excess soil, then reset the clean cycle. If the fault code reappears, contact an authorized servicer. | |
There are no beeps and no display. | • Oven may be in Sabbath Mode. |
Noises may be heard. | • The oven makes several low level noises. You may hear the oven cooling fan going on and off. You may also hear the oven relays as they go on and off. These are all normal. |
• As the oven heats and cools, you may hear sounds of metal parts expanding and contracting. This is normal and will not damage your appliance. |
F8e0 Error Code On Whirlpool Range
Jenn-Air W2451 oven error codes
F8e0 Error Code Jenn-air
FAULT CODES | PROBLEMS | COMPONENTS TO CHECK |
---|---|---|
F1 | POWER TO ELEMENT RELAY ENERGIZED DURING TIME OF DAY DISPLAY. | J2 harness shorted. If checks ok, change (PRB) power relay board. Note: For double oven only, change second oven board. |
F2 | Over temperature sensed; over 620 sensed by control in time of day mode, bake mode, or over 950 sensed in clean mode. | Ohm sensor. If checks ok, change power relay board. |
F3 | Cooling fan on with no oven function selected. | Ohm sensor, wire harness to sensor. |
F4 | Shorted oven sensor | Ohm sensor, wire harness to sensor. |
F5 | Power element relays disabled in cook mode. | 1) Intermittent sensor or wire harness connection. 2) Intermittent contact on PRB. |
F7 | Shorted key sensed for 32 seconds | 1) Membrane shorted 2) Display Board |
F8 | Shorted meat probe alarm. | 1) Probe jack or harness to probe jack. 2) Probe sensing temp. Above 250 F. |
F9 | Door lock safety circuit on power relay board sensed. | PRB |
FF | Invalid temp. Reading on PRB. | Check sensor and harness, PRB. |
F- | Communication error between boards. | J2 harness, ohm wires end to end. Harness ok, replace display board. |
FC | Communication error between boards. | J2 harness, ok, replace PRB. |